Changing attitudes and regulations are making efficient, long-lasting operation more important than ever for Energy from Waste plants (EfW). Martin Trenk, Head engineer for Boiler coatings and EfW applications at Castolin Eutectic, explains.

Trenk Martin
To fulfil the role of baseload in the power generation mix, thermal power plants must prioritise consistent power output. Maintaining consistent operation and output is a particular challenge for EfW plants, whose fuel – municipal waste – does not necessarily always yield the same amount of energy per tonne. The last thing an EfW plant operator wants, while closely monitoring and finely calibrating the boiler temperature and turbine speed, is an unplanned stoppage.
Yet many EfW plants do contend with frequent stoppages, both planned and unplanned, to replace worn parts or to mitigate emissions. With the European Union tightening its rules around burning municipal waste, EfW operators need to prove their plants can be efficient and play their assigned role in their nations’ power systems. It’s a question of industrial sustainability.
Which is why Castolin Eutectic has its own role to play in the EfW industry. Pioneering Industrial Sustainability is a long-held philosophy of Castolin Eutectic, one that has driven more than a century of innovation to improve the lifespan and efficiency of industrial parts – both outcomes with the potential to reduce the number of stoppages EfW plants need to endure.
Waste handling – unpredictable abrasion and wear
Most EfW plants burn mixed municipal waste that would otherwise be sent to landfill. The waste can include food, paper, textiles, wood and plastic – but also significantly more abrasive materials like metal, glass and electronic waste.
Because the different materials present can yield widely different amounts of energy, it is important to mix the waste well before incineration, to achieve a stable boiler temperature. All this naturally causes significant wear on the hoppers the waste is delivered into, the crusher rotors that mix and break it up, and the apparatus that conveys it to the incinerator (which may be a grabber or a screw, depending on the plant design).
Not only can the wear on these fuel handling parts be significant, but it is also often unpredictable, because the fuel loads are not uniformly abrasive. The composition of the waste being sent to EfW plants can vary considerably depending on the composition and habits of the feeder municipalities, and even on the season. However well mixed the waste is, some loads will contain more glass, metal and hard plastic, and some will contain less.
This has historically posed an economic conundrum for EfW plant builders, owners and operators. A plant’s waste handling systems ideally need to be hardwearing enough to stand up to significant abrasion – but may not need to be that hardwearing a hundred percent of the time.
If the plant handled only the most abrasive materials, the case for up-front investment in harder-wearing parts would be obvious: the plant would be unable to operate for long without them. But because not all of the fuel is significantly abrasive, and because not all plants are costed on a life-cycle basis, it can be tempting to gamble on less hardwearing parts. If the loads they handle happen to be mostly less abrasive, they might outlast their designed service life.
But it could also go the other way. And when it does, a planned stoppage in six months’ time can become an unplanned stoppage tomorrow, bringing with it all the challenges of quickly and safely shutting the incinerator and turbine, and later ramping back up to a stable boiler temperature.
A typical example of the difference that wear protection can make is on fuel crusher rotors that needed to be rewelded on a yearly basis because of high wear. In many cases the crusher casings are also affected by wear. An effective solution is refurbishment with SAFE-HARD 600 Chromium free welding wire applied to the rotor, while a composite material known as CastoDur Diamond Plate (CDP) is applied to the casing. The result is that the lifetime of the crusher is always increased, but the level depends on the type of waste. The improvement can range from 2 up to 10 times the life without wear protection.
The very abrasive fuel in waste to energy plants also creates wear issues for hydraulic garbage grabs. As the edges wear away, more waste falls back into the bunker. This leads to the need for more lifting movements and more energy and time required for fuel filling. The solution is to fit CDP wear plates on the inside of hydraulic garbage grab. The outcome is a 200% increase in lifetime.
Case study: Boiler coatings – ChromeClad
In March 2021, Castolin Eutectic perfomed a boiler coating job at a chemical plant in Germany, applying wear protection on 740 m² of boiler panels. More than one year later, in November 2022, the exposed surfaces were still visually flawless. The solution applied through Twin Wire ARC Spray was a coating called ChromeClad XC, a nickel-based coating providing superior resistance within extreme corrosive environments. The proprietary alloy top coat is applied over an extremely dense bond coat which literally seals the weak ferrous substrate and ensures excellent bonding. Subsequently, a ceramic layer called TubeArmor, is applied over this coating to densify it and prevent slag build-up. It is a non-porous, non-reactive shield that resists ash, oxidation, erosion, iron sulfide corrosion, sulfur and chlorine permeation and hazardous chemical byproducts. TubeArmor is applied on the prepared surface one coat at a time until the recommended thickness is achieved. Its green color is a perfect indicator that provides excellent contrast for drone inspections. As a result of TubeArmor’s high emissivity, significantly more heat can be absorbed in areas where it is needed than, for example, cleaned surfaces clad with Inconel. |

Water walls protected with TubeArmor LT
Ash handling – time to raise the industry standard?
Not all the waste delivered to EfW plants is combustible. Non-ferrous metals and some other non-combustible materials form slag, which must be removed from the incinerator along with ash.
In most EfW plants, the chutes, chain conveyors and sieves of the ash handling system are manufactured from steel or manganese steel. Without protection from additional plating or specialist coatings, these industry standard parts are vulnerable to high abrasion wear from the ash and non-combustibles in the slag. Manganese steel de-slagger chutes and slag-sorting sieves usually need replacement after only a year in operation.
Why are EfW plants still being constructed as standard using parts that cannot stand up to the normal stresses of their operations? Using harder-wearing materials or adding wear-facing solutions for materials like manganese steel, would undoubtedly increase the up-front investment needed to construct an EfW plant – but the historical performance of these standard parts suggests strongly that these up-front costs would pay off over the life cycle of the plant.
One example of the possibility for improvement is found in the high level of wear on the gliding strips, the chain and depending on the construction also on the bars, which are made normally from standard or manganese steel. This is due to ash and non-combustibles in the slag. The solution is to use cut CDP plates for the strips and bars. The Chromium carbides and Borides content provides protection against abrasion and reduces friction and consequently wear of the chain. The result is that the lifetime for strips increases up to 10 times, for the bars up to 6 times.
Flue gas cleaning – the influence of attitudes and regulation
As well as the engineering challenges of incinerating unsorted municipal waste, EfW plants must deal with changing attitudes to waste among regulators, businesses and the public. These trends do not progress uniformly in all territories, so EfW operators in different parts of the world face different challenges. However, the direction of travel for the world as a whole is tending towards:
- reduced carbon dioxide and equivalent emissions
- a circular economy, featuring increased recycling and reuse, and so less waste being sent to landfill and EfW
One significant consequence of increasing enthusiasm for recycling and reuse is that people throw away less plastic. The caloric value of plastic is high relative to many of the other types of waste that EfW plants use as fuel. So, when people try to throw away less plastic, the overall caloric value of local EfW plants’ fuel starts to fall.
As established, it is vital for EfW plants to maintain a stable boiler temperature, and therefore a steady turbine speed and energy output. With less energy available in the fuel being delivered, EfW plants must use bigger fuel loads to obtain the same energy output.
At the same time, operators must keep close watch on their plants’ emissions. The European Union regulates emissions from all thermal power plants and has specific rules about allowable emissions from incinerating municipal waste. For example, if the percentage of particulates emitting from an EfW plant’s flue exceeds the allowed limit, the plant must shut down to investigate and mitigate the cause.
To protect the environment and avoid these unplanned regulatory stoppages – which compound planned and unplanned stoppages to replace worn parts, further reducing a plant’s annual uptime – EfW plants incorporate flue gas cleaning systems, which combine filters, cooling and chemical processes to capture particulates and harmful gases from the incineration process before they can be emitted to the atmosphere.
Because their purpose is to process hot, acidic exhaust gases, these crucial systems are prone to various forms of corrosion, as well as erosion by fly ash carried in the flue gas. Wear and damage to the flue gas cleaning systems can reduce their effectiveness, potentially leading to regulatory stoppages on top of the stoppages needed to replace the damaged parts themselves.
A key area for attention is the flue gas deflectors that get damaged by erosion due to fly ash particles in the flue gas at around 170˚ C within a year. Covering the deflectors with a laser cladded LC8 half pipe provides protection against erosion by the fly ash particles. When assessed after a year in operation no damage was found.
The priority for EfW – extending service life
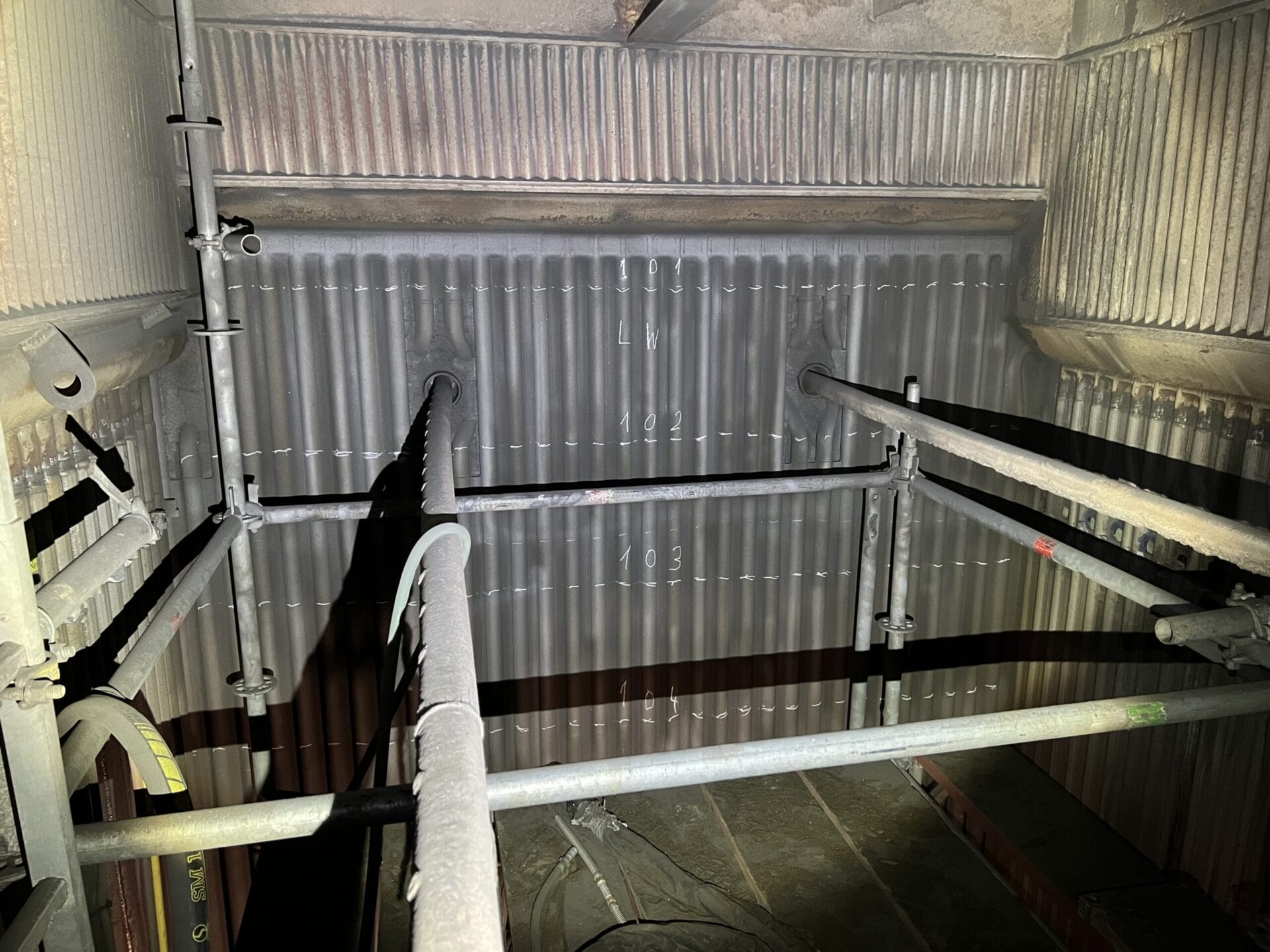
ARC sprayed side wall
It is more important than ever for EfW plants to operate as efficiently as possible.
Efficiency means extracting the maximum energy possible from each hopper of fuel, to compensate for its decreasing plastic content and caloric value.
And efficiency means operating at a stable boiler temperature, turbine speed and energy output for as much of the year as possible, with stoppages – planned or unplanned, for repairs, maintenance or regulatory reasons – kept to a minimum.
To achieve this, EfW plant operators must prioritise extending the service life of parts throughout their plants. Parts that last longer before wearing out will cut down on stoppages for maintenance and repairs. And parts that perform at peak for longer will maintain the efficiency of the plant’s systems, converting more waste to energy, cleaning up the flue gases more successfully, and reducing the chance of regulatory stoppage and damage to the environment.
Castolin Eutectic is determined to support the EfW industry in its mission to reduce landfill, make good use of waste and protect the environment. The company’s global network of technical advisors takes a whole life-cycle approach that maximises the efficiency of systems, the service life of parts, and long-term cost-effectiveness.
From fitting CDP strips and wear plates to waste handling apparatus, to arc-spraying waste incineration and flue gas cleaning system components with heat- and corrosion-resistant coatings, Castolin Eutectic offers solutions for every element of a modern EfW plant. Case studies show that customers in this sector have seen the service life of waste grabbers double, and fuel ducts and grate bars operate for eight years and counting with very low wear, after being enhanced with Castolin Eutectic wear-facing solutions.
Staying power
EfW plants already in operation need to make the most of upcoming scheduled maintenance periods to apply wear-facing solutions to extend the life of parts in service.
And for any new EfW plants currently in the planning stages – now is the time to rethink the accepted industry standards, in light of the real-life experiences of existing plants, and build these systems to last.
For further information: https://www.castolin.com/recycling