Corrosion in its many forms, costs both private and public sectors hundreds of billions a year to repair or replace electrical, electronics, or avionic components because of failures caused by corrosion. Lost productivity and revenue caused by plant and equipment corrosion is a serious matter. While all metals corrode, due to a number of different factors, there is no simple or single solution to the overall corrosion problem. However there are some very cost effective and proven ways to prevent corrosion and failures caused by corrosion and thereby reducing or eliminating associated costs and increasing safety which should be foremost in the mind set of any preventative maintenance programme.
Electrical and electronic equipment and components that are used in adverse environments, e.g. the oil and gas industry, waste-water treatment plants and the pulp and paper industry, where corrosive gases such as hydrogen sulphide can be found, cause severe corrosion and the rapid deterioration of the electronic components and equipment including connectors and switches used in these and other work environments. Preventing hydrogen sulphide (H2S) corrosion in electrical and electronic equipment involves a combination of preventive measures and material selection. Here are some steps to mitigate H2S corrosion:
Protective Coatings:
An essential corrosion preventative measure is to apply coatings to vulnerable components. One such coating is SuperCORR A advanced lubricant and corrosion inhibiting compound. It will help prevent H2S corrosion in electrical and electronic equipment, ensuring their longevity and reliability in environments where H2S exposure is a concern.
Material Selection:
Choose materials that are resistant to H2S corrosion. For example, stainless steel, nickel alloys, and certain plastics are less susceptible to corrosion by H2S compared to carbon steel.
Enclosures, Sealing and Ventilation:
Seal electrical and electronic equipment and cables in airtight enclosures to prevent H2S exposure. Ensure these enclosures are made from corrosion-resistant materials. Implement ventilation systems to reduce the concentration of H2S in the equipment’s environment.
Monitoring and maintenance:
Regularly monitor H2S levels in the environment where the equipment is installed. Install gas detectors to provide early warnings of increased H2S concentrations. Perform regular maintenance checks on equipment to detect any signs of corrosion. Replace any corroded components promptly.
Design Considerations:
Consider the design of the equipment and its surroundings to minimize the likelihood of H2S exposure. For example, elevating equipment above potential H2S sources can reduce corrosion risk.
Education and Training:
Provide education and training to personnel working with the equipment on the risks of H2S corrosion and the importance of preventive measures.
Emergency Response Plan:
Develop an emergency response plan in case of H2S exposure or equipment failure due to corrosion. This plan should include procedures for evacuating personnel and shutting down equipment safely.
SuperCORR A specialist barrier film corrosion protection
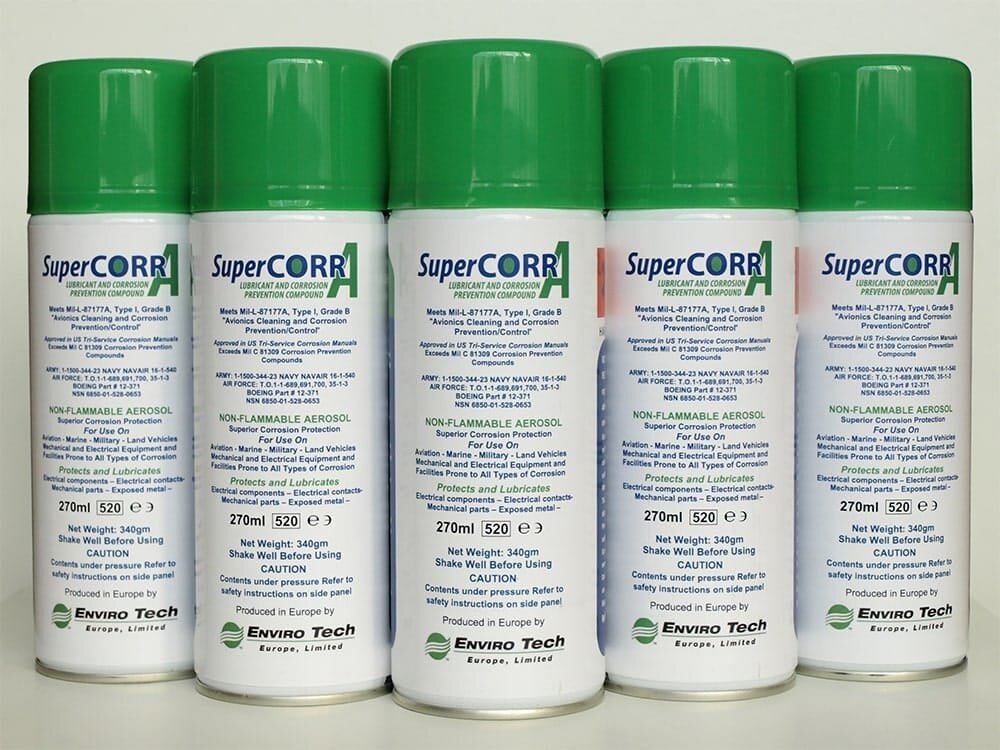
EnviroTech Europe supplies advanced corrosion protection products, based on approved synthetic materials, to provide quality solutions to a diverse range of lubrication and corrosion problems.
SuperCORR A is a unique and proprietary formulation with long-lasting, anti-corrosion inhibitors providing a superior lubrication coefficient and protection against moisture, wear, general and fretting corrosion, static electricity, corona, and other electro migration problems. The non-flammable film is only 7 microns (0.007mm) in thickness, is not a wax or oil-based product and is formulated without sulphates, chlorides, petroleum-based material, or halogens, to meet the EU RoHS directive.
The use of SuperCORR A for corrosion protection can not only bring financial savings in reduced maintenance and replacement costs but more importantly greater safety. It is much simpler and a lot less costly to prevent corrosion than to repair or replace the damaged equipment or component that failed because of corrosion.
SuperCORR A is a proven and cost-effective way to prevent or inhibit corrosion from destroying electronics and electrical components. It was specifically designed to lubricate and prevent corrosion in electrical fittings and connectors; electrical and avionic harness assemblies and connectors; electrical and electronic switches; close tolerance and dissimilar metal components; lighting connectors and sockets. A unique non-flammable “self-healing” ultra-thin film lubricant with a proprietary corrosion preventive compound that will not harden or crack, is not a wax or oil-based product and is formulated without sulphates, chlorides or halogens.
SuperCORR A also inhibits corrosion caused by exposure to both fresh and salt water moisture as well as the corrosive vapours from Sulphur dioxide (SO2), Nitrogen dioxide (NO2), Hydrogen Sulphide (H2S), Ammonia (NH3), and Chlorine (CL12) based gases found in waste water and sewer treatment plants, pulp and paper mills and plants, chemical and petroleum plants, maritime industry, aircraft/airline industry, military equipment including ships, aircraft, and rolling stock, auto industry, farming and agriculture industry, and the list goes on.
SuperCORR A is packaged in aerosol cans making application to component parts easy for engineering crews in difficult locations and conditions. Unpainted mild steel will not rust on exterior surfaces directly exposed to sea water environments for at least 6 months, protecting electrical connectors, switches, chains, drive shafts from corrosion while maintaining lubrication on moving surfaces.
EFFICIENT AND ECONOMICAL
Extremely long-lasting, specially formulated and proprietary anti-corrosive inhibitor.
- Eliminates premature failure of components created by moisture, general or fretting corrosion.
- Prevents deterioration and contamination on all surfaces of electronic and electrical equipment and mechanical close tolerance moving components.
- Reliability increased, maintenance intervals increased, costs reduced, manufacturers save costly warranty service calls or product re-call.
HISTORY
SuperCORR A was originally developed for the U.S. Air Force to comply with military specifications and to prevent electrical and electronic components from systems failures caused by corrosion. It became the industry standard for avionic corrosion protection within MROs (maintenance, repair and operations) and OEMs (overhaul and original equipment manufacturers). It’s unique ability to displace water and provide a performance enhancing level of corrosion protection has led to it being used in many other applications and industries worldwide.
FURTHER INFORMATION
Please visit our website https://www.envirotech-europe.com/supercorr-a for information about other uses and applications for SuperCORR A.
For more advice, please telephone us on +44 (0) 20 8281 6370 or use our website contact form. Manufactured in the United Kingdom and available on short delivery times through our dedicated team of distributors worldwide.
supplied and supported by

EnviroTech Europe Ltd
Steward House, 14 Commercial Way,
Woking, Surrey GU21 6ET,
United Kingdom
Tel +44 (0) 20 8281 6370
www.envirotech-europe.com | contact@envirotech-europe.com