Manufacturing is one of the UK’s success stories. With an output valued at £224bn[1], we are now the eighth largest manufacturing nation in the world. But our position is vulnerable unless we significantly increase our level of automation.
Helping manufacturers to increase their productivity, reduce waste, improve product quality and alleviate labour shortages, the benefits of automation are myriad. And as the only G7 country to sit outside the top 20 in terms of robot density (we are actually 25th in the IFR global robot league table), accelerating our automation uptake is essential if we are to retain our place as a leading manufacturing nation.
It is therefore important that when designing a new product, planning a new production line or upgrading your existing facility, automation is factored in from the very start of the process, not just as an afterthought. Not only does this keep down costs, it also ensures that any automation will be right first time, minimising downtime, boosting productivity and resulting in a solution that is fit for purpose.
Here, Oliver Selby, Head of Sales for FANUC UK, outlines six key design considerations for seamless automation integration…
- Embrace the automation process
It may sound obvious, but keep front of mind the fact that your product’s manufacturing process will need to benefit from automation. This can generally only be done by incorporating automation into the design of the product, whether that’s by giving the part a feature that allows it to be picked up by a robot, located or inspected by a vision system, or allowing access for a welding torch or fixturing, for example.
This mindset also translates to the wider production line. We see products designed using multiple materials, joining techniques and production methods which won’t all necessarily work together to produce something that is easily automated, but which designers are reluctant to give up. However, it can be better to take a hit on one material or process to make things easier to automate, thereby reducing overall production costs.
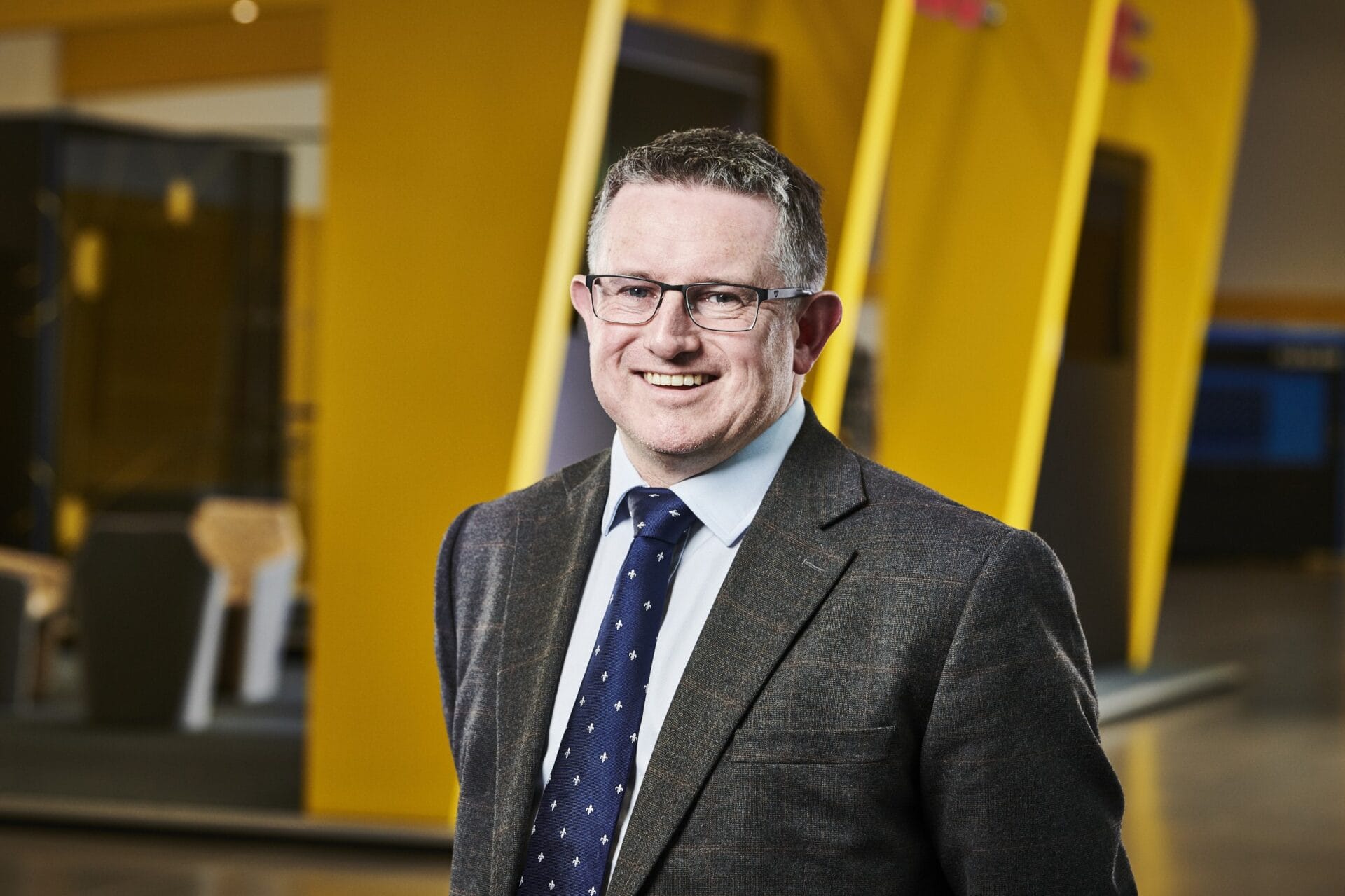
Oliver Selby, Head of Sales for FANUC UK.
- Prioritise parts
Focus on part delivery methods within the complete solution. Often, customers will come to us looking for an automated solution, but with their component parts delivered in no ordered way. As much as 20-30% of the cost of the project can be spent on getting those parts located or fixtured and ready to process before the real automation process can actually begin. It makes more commercial sense to keep parts in order, whether that’s in a nested box, on a conveyor or in a stack.
Also think about part handling and fixturing. Significant costs could end up being channelled into part fixturing – even more so if you are working with a range of parts due to multiple fixtures. A good example of best practice here is to focus on one-way assembly; for example, where parts stack on top of each other to create the complete product or common part features that allow common fixturing.
- Consider TCO
Concentrating on the wrong drivers for automation is a major error but one that we sadly see all too frequently. Some customers are more focused on fitting an automation solution into a defined payback period (often under two years) instead of looking at the value it will bring to the business over its lifetime. A total cost of ownership model is a far better measure. Purchase price only accounts for between 15-25% of the total cost of ownership; the remainder is made up of factors such as maintenance, energy usage, repairs, and even end of life. Measuring TCO rather than ROI will ensure you get the right automation solution for your business, resulting in real long-term value.
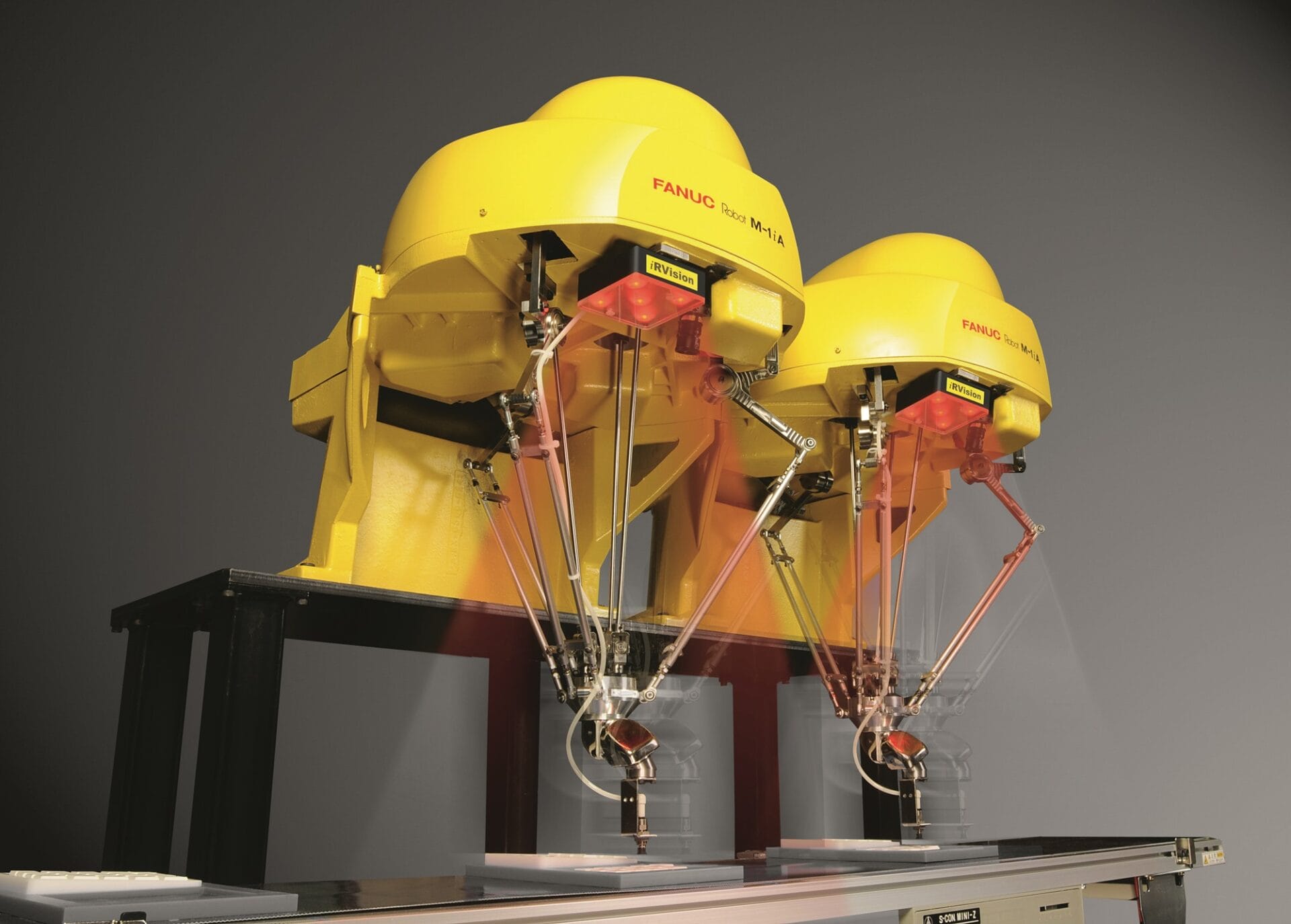
Incorporate automation into the design of the product, whether that’s by giving the part a feature that allows it to be picked up by a robot, located or inspected by a vision system.
- Remember the process, not just the consumer
It can be tempting when developing a new product to prioritise what’s easiest for the consumer, without realising that this may negatively impact the automation process. A prime example of this is shelf-ready packaging. The current trend within food manufacturing for front-facing packaging with tear-off flaps or loose fitting lids allows retailers quick and easy restocking of shelves. However, this seemingly simple change in packaging design has made it extremely difficult for automation to be exploited for end-of-line palletising, as the loose fitting lid or tear-off flap is not conducive to staying in place. Therefore, before making any packaging changes – no matter how seemingly minor – think carefully about how they may impact your ability to automate, and the effect this will have on production efficiency and labour demand.
- Talk to automation suppliers
Engage with automation suppliers as early as possible. At FANUC, we are more than happy to support designers that are beginning their journey towards automation and will readily provide guidance on what the process is going to involve. We’ve done this countless times throughout the years as different sectors have started to embrace automation – from manufacturers of low-cost products to high-value goods; companies in the food industry; and more recently, with EV battery manufacturing for the automotive sector. We have rounded experience across lots of different applications within a wide range of industries that we are happy to share, and which designers can learn from.
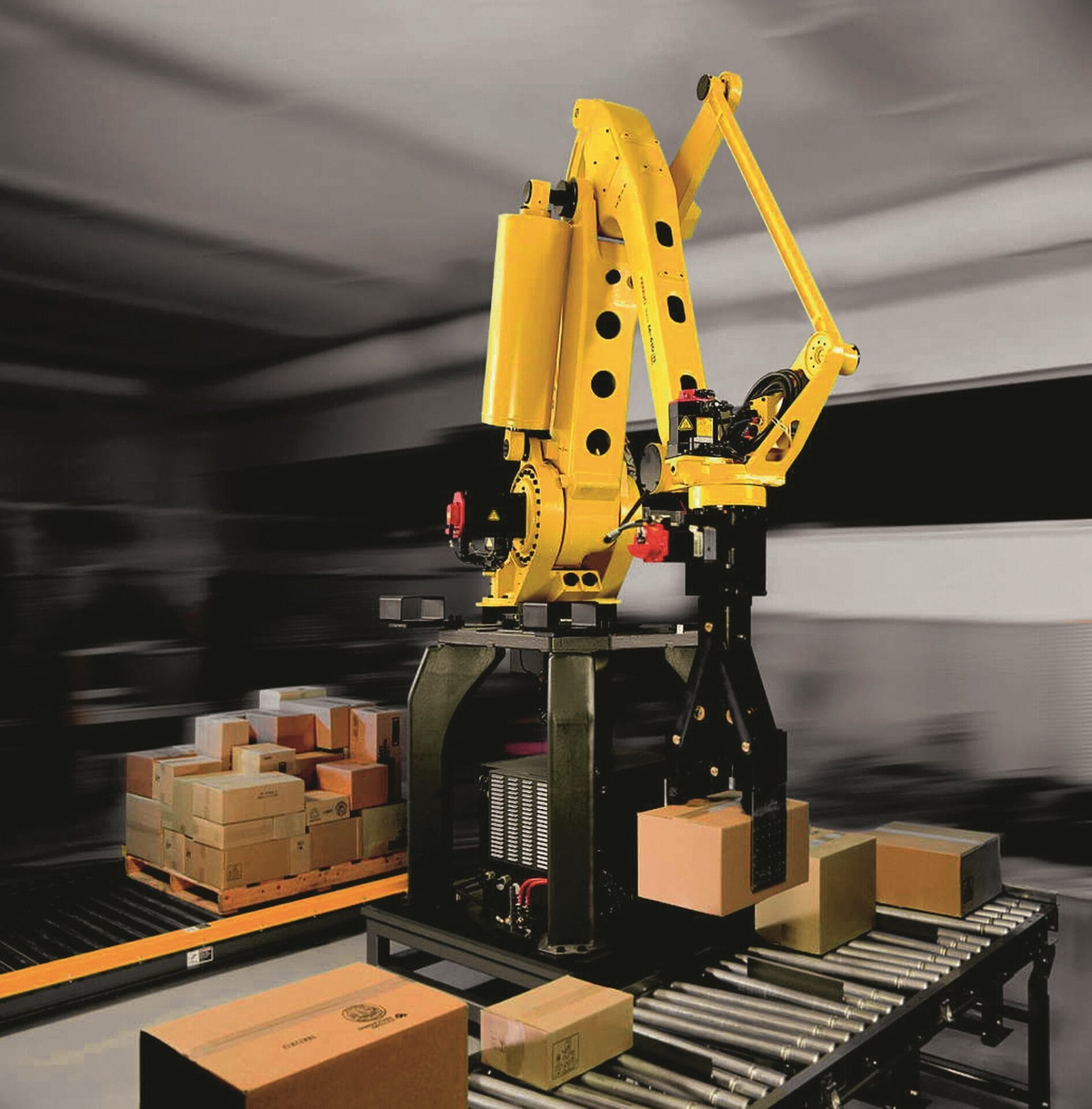
Robots as a Service (RaaS) is a subscription-based option that enables manufacturers to pay a set fee over a specified period of time, and effectively lease a robot to use in their facility.
- Try before you buy
Finally, as in many industries, some automation suppliers are now starting to offer low-cost/low-risk routes into automation for companies taking their first steps into automation. Robots as a Service (RaaS) is a subscription-based option that enables manufacturers to pay a set fee over a specified period of time, and effectively lease a robot to use in their facility. The limitation of this offering is that it will only suit certain simple applications, for example, palletising, or particular welding options. The upside is that the robot can be repurposed for multiple product types – palletising a box of cakes is effectively the same process as palletising a box of dishwasher tables, for instance. Talk to your automation supplier to determine if RaaS could be right for your needs in the short-term – by allowing firms to test the water and experience the benefits before making their own investment, it can represent an affordable route into automation for some first-time users.
In conclusion, when designing or upgrading any production line, make sure to consider automation as one of the cornerstones of your project from the outset. By working with a reputable automation supplier, you can ensure your manufacturing facility is optimised for success, not just for today, but for years to come.