A UK-based technology specialist has signed a new international deal that will see additive manufacturing used to make complex concrete moulds.
Rapid Fusion, which provides full turnkey 3D printing solutions from its R&D centre in the South West, has used its ZEUS 3D robotic system to create intricate concrete pieces for Italian start-up Nanoo.
The complex moulds were used to create table legs for an exclusive Italian furniture manufacturer and took just a few days to make – compared to almost two weeks using conventional methods.
By using additive manufacturing – along with a built in CNC milling tool – the two companies were able to achieve precision quality whilst reducing expensive labour costs and, due to using recycled PET-G, enhance the sustainable performance of the project.
This landmark contract has given Rapid Fusion and Nanoo the ideal test case to prove to the construction sector that 3D printing can work for bespoke moulds commonly used in large projects, to create free form facade elements, complex concrete structures and elements of furniture designed by world-leading architects.
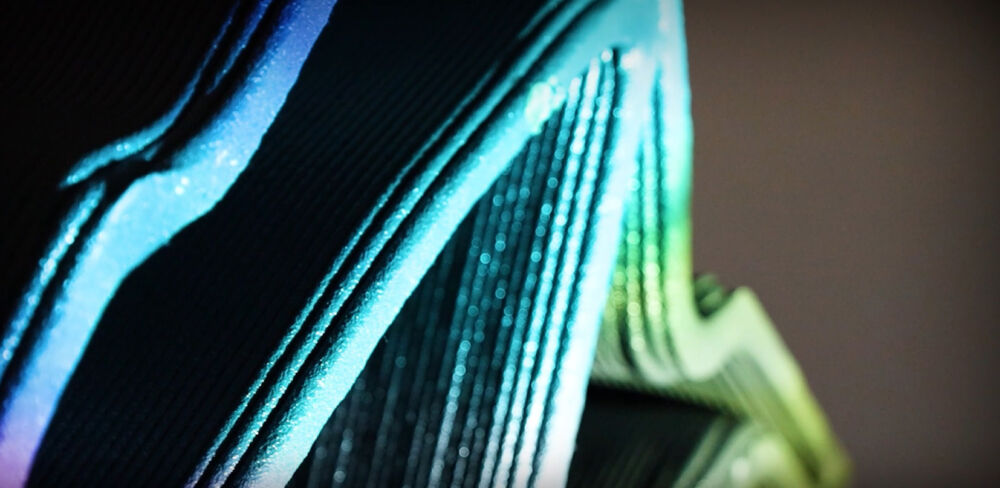
The test was conducted on a relatively small scale but has allowed the two companies to validate the idea, production time, accuracy, and behavior of advanced cementitious materials, such as UHPCs and related release agents in conjunction with a PET-G mould.
Additional trials are currently being completed to find out how many times the mould can be reused without any maintenance being required and there is genuine confidence that it can exceed 100 uses.
“Construction is an industry facing increased pressure to innovate, optimise costs and reduce environmental impact…switching to additive manufacturing for some of its moulds helps them deliver on these objectives,” explained Martin Wood, Director of Sales at Rapid Fusion.
“We have proven with our partners at Nanoo that large-format robotic 3D printing offers a faster, more sustainable, and cost-effective solution to the challenges faced by traditional concrete mould production.”
He continued: “Another key benefit is the reduction of waste, with those made from composites often producing a lot of excess, not to mention the moulds being discarded after use and the environmental degradation that then occurs.
“3D printing uses recycled materials and can be reused once the mould is done with. That’s a massive sustainable benefit for construction.”
Rapid Fusion, a sister business of 3D printing hardware specialist EVO 3D, is committed to becoming a major player in global additive manufacturing platforms – all designed, built and assembled in the UK with the recent bonus of ‘Made in Britain’ certification.
It launched its first bespoke cell, Apollo, earlier this year and this has already received significant interest for its ability to offer faster speeds than existing FDM printers (nearly 200 times quicker).
The company is now just a few months away from officially releasing a second cell called ZEUS that will include the CNC milling tool and provides precision milling and post-processing of polymer 3D parts.
Martin continued: “Automotive, aerospace, medical and renewables have all been sectors traditionally suited to what additive manufacturing can deliver. We knew this could be transferred to the world of construction and, thanks to our first deal with Nanoo, we are producing complex moulds being used in real world applications.
“In fact, our Italian friends have been that impressed with the results they have just signed on the dotted line to take delivery of a ZEUS system, one of the first in the world to be deployed.”
Mirko Scaburri, founder of Nanoo, added his support: “This is an interesting partnership that is working because we are playing to each other’s technical strengths in exploring how we can design and manufacture concrete moulds using large format 3D printing.
“Now that Rapid Fusion has created ZEUS, we have the ability to print and then CNC mill away any excess layers, which could have been a barrier. Instead, the customer now gets a mould exactly the way they want it, in days rather than weeks and at a comparable cost.”
He concluded: “I work with a lot of big construction companies and architects and this technology is really creating waves in the sector. The latter especially like the additional design geometries they can achieve with additive manufacturing – that is a big sell for them.”
Martin concluded: “A lot of our work is in R&D and pushing the boundaries of what is possible. Working with Nanoo, we have developed a positive mould solution that has the potential to transform the construction industry.”
For further information, please visit www.rapidfusion.co.uk or follow the company across its social media channels. More detail on Nanoo can be found at www.nanoo.cc or at www.linkedin.com/company/nanoo-cc.