An automated solution comprising eight FANUC robots has enabled an Athens-based pharmaceutical manufacturer to run an uninterrupted 24/7 production line, boosting throughput and cutting production costs. DEMO SA, Greece’s leading producer of injectables, has successfully automated the loading and unloading processes around its tray-based sterilisation of plastic containers and bags, employing a series of FANUC industrial robots to overcome challenges surrounding differing sizes, dimensions and handling requirements.
Established in 1965, DEMO SA manufactures a range of injectable drugs from its base just outside Athens, exporting to 85 countries worldwide. Hospitals and other medical organisations around the globe rely on the company to provide products in a timely and efficient manner, while maintaining the highest standards of quality. In recent years, it has embraced robotics in order to meet these exacting demands, automating several production and packaging lines with the help of its long-term industrial equipment partner, SABO SA. As a long-standing strategic partner of SABO, FANUC has provided robots for a number of DEMO’s previous projects and was once again the obvious choice for this latest installation.
“We chose SABO for our new automation project because of their experience and because they use FANUC robots,” explains DEMO SA’s Technical Director, Argyris Lellos. “We prefer FANUC equipment: to date, we’ve automated four production lines using a total of 12 FANUC robots.”
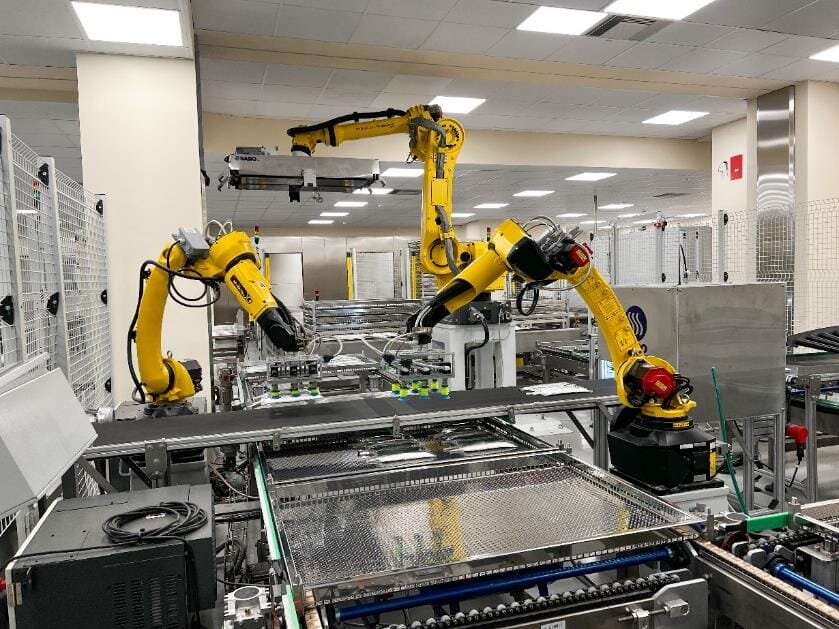
SABO also installed two larger R-2000iC/165F 6-axis robots for handling the trays as well as two smaller FANUC M-10iD/12 robot arms (pictured at the front).
Meeting strict hygiene standards
The latest production area that DEMO was looking to automate concerns the sterilisation of plastic containers and bags in tray-based systems. After cleaning, DEMO fills the plastic ampoules with injectables, while the bags carry sterile solutions, so the need for the highest levels of hygiene was paramount for any proposed automation solution.
In addition to meeting superior hygiene standards, the robots would be required to perform a range of different loading, unloading, picking, placing and transporting operations involving the trays, containers and bags. The variety of tasks within this project led to FANUC specifying a total of eight robots spanning four different models.
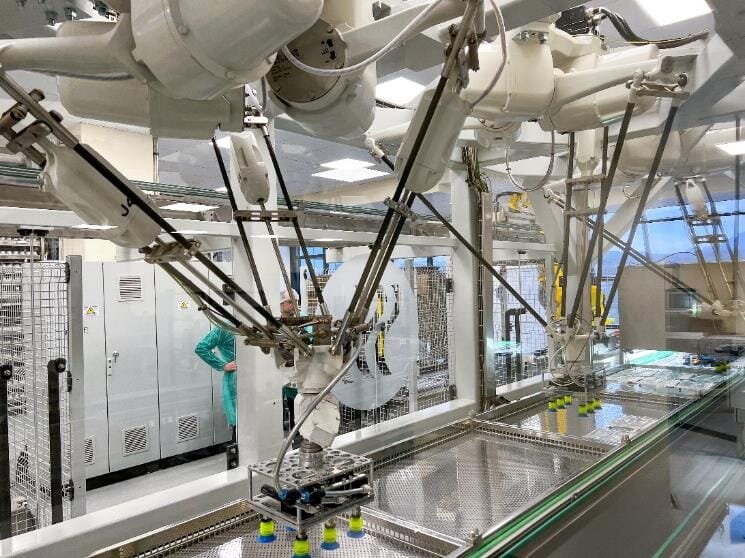
The DR-3iB/8L delta robots use end-effector suction cups for handling the bags at very high speeds.
Speed and accuracy
“For the task of loading and unloading the plastic containers into and out of the trays we selected a FANUC M-710iC lightweight 6-axis robot,” says Angelos Markou, Sales Manager Industrial Solutions at SABO SA. This robot works at pace, using a SABO-designed end effector to transport and place/remove multiple plastic containers in a single lift.
SABO also installed two larger FANUC 6-axis robots for handling the trays; R-2000iC/165F models, which can lift payloads up to 165 kg and operate in tight spaces. The newly automated production line also features two smaller FANUC M-10iD/12 robot arms and three FANUC DR-3iB/8L delta robots. The latter use end-effector suction cups for handling the bags at very high speeds.
“FANUC robots are reliable products,” says Markou. “But also important is the company’s after sales support, which is very quick and efficient.”
Improved productivity
For DEMO’s Argyris Lellos, the main benefits of this latest automation project were clear from the start: “We now have 24/7 uninterrupted production, with faster throughput, reduced production costs and less downtime. We’ve also saved space due to the small footprint of the robots. Further advantages include a better working environment for our employees and a very flexible and easy-to-use operator interface. We are now relying on SABO and FANUC for our future automation projects.”