Nick Allen, Managing Director, 3DPRINTUK
Quality control is paramount in additive manufacturing (AM), particularly when it serves as a production technology. Unlike traditional manufacturing methods, where defects can often be visually detected and corrected, AM operates on a layer-by-layer basis, making it imperative to catch errors early in the process. Any deviations in material properties, printer calibration, or design specifications can result in defective products, compromising functionality and in some cases, even posing safety risks. In mission-critical industries such as aerospace, marine and medical, where precision and reliability are non-negotiable, the consequences of inadequate quality control can be catastrophic, ranging from equipment failure to patient harm. Robust quality control protocols in AM are essential to ensure consistent, high-quality parts, minimise waste, and guarantee the reliability and safety of end use products.
Moreover, in production settings, maintaining quality control is essential for cost-effectiveness. Inaccurate or inconsistent 3D prints can lead to scrapped materials, increased production time, and costly rework. These inefficiencies can erode profitability and competitiveness. Robust quality control processes enable manufacturers to identify and rectify issues promptly, reducing waste and optimising resource utilisation. By focusing on quality control in AM, businesses such as 3DPRINTUK can uphold their reputation for delivering reliable, high-quality products for customers while simultaneously improving operational efficiency and ensuring their long-term success in an increasingly competitive marketplace.
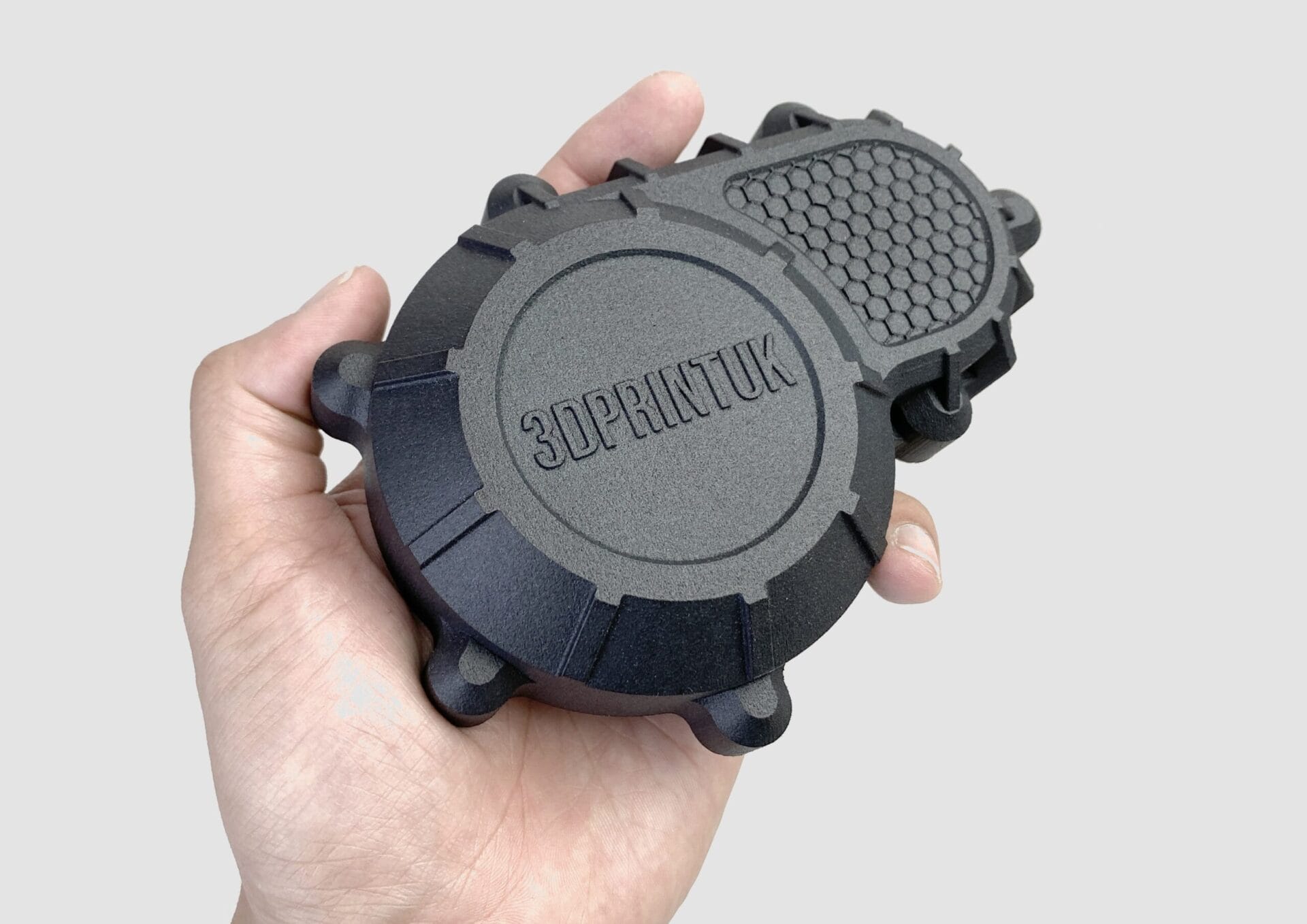
3DPRINTUK operate to ISO 9001 and 14001 standards
KEY QC CONCERNS IN AM
Quality control in AM parts is critical due to several key issues that can significantly impact end-use functionality. Firstly, dimensional accuracy and warping are common challenges. Variations in temperature, cooling rates, and part geometry can lead to warping and distortion during the printing process. This can result in parts that do not meet the required tolerances or fit together properly, impacting their functionality in assemblies or causing issues in applications where precision is essential.
Second, material properties and consistency are vital. The quality and consistency of the plastic material used in AM can vary, affecting the mechanical, thermal, and chemical properties of the final part. Inconsistent material properties can lead to unpredictable performance, making it difficult to ensure that parts meet the necessary specifications for their intended use. These quality control issues in additively manufactured plastic parts can have a cascading effect, compromising the overall functionality and reliability of end-use products, and underline the necessity of rigorous quality control measures in this manufacturing process.
Finally, layer adhesion is a crucial concern especially with technologies such as Fused Deposition Modelling (FDM). In AM, parts are built layer by layer, and inadequate adhesion between layers can lead to weak bonds, reducing overall part strength and durability. This can result in parts that are prone to delamination or cracking under stress, compromising their functionality and reliability.
ADDRESSING QC CONCERNS
Ensuring the quality of AM parts requires a combination of techniques and strategies to address various aspects of the printing process. Calibration of the system(s) being used is fundamental to achieving precise and consistent results. Regularly calibrating and maintaining the 3D printer ensures that it operates within specified tolerances.
Choosing the right plastic material is also crucial for achieving desired mechanical and thermal properties. Materials need to be sourced from reputable suppliers and users such as 3DPRINTUK should perform quality checks to ensure consistency. Material testing, including mechanical property characterisation, can help validate material suitability and identify potential variations that may affect part quality. In addition, real-time monitoring of the printing process can identify issues as they occur. Techniques such as in-situ sensors, thermal imaging, and computer vision can be employed to monitor factors like temperature, layer adhesion, and print speed. When deviations are detected, the printer can make automatic adjustments or trigger alerts for manual intervention, ensuring consistent print quality.
After printing, post-processing steps like surface smoothing, support removal for some AM processes, powder removal for processes such as SLS, and heat treatment can improve the final part’s aesthetics and mechanical properties. Additionally, comprehensive inspection methods, including visual inspection, 3D scanning, and non-destructive testing (NDT) techniques are critical for verifying part quality, dimensional accuracy, and structural integrity.
Finally, maintaining detailed records and documentation throughout the AM process is essential. This includes recording parameters such as print settings, material batches, and inspection results. Such records are invaluable for traceability and quality control audits, helping identify any trends or deviations in production that may require corrective actions.
Rigorous QC & machine maintenance is the only way to deliver part accuracy and consistency.
CONTINUOUS IMPROVEMENT
So, it can be seen that ensuring the quality of AM parts is a multifaceted process that involves precise printer calibration, careful material selection and control, real-time process monitoring, thorough post-processing, and diligent record-keeping. Combining these techniques allows bureaux such as 3DPRINTUK to produce parts that meet or exceed the required specifications, ensuring their functionality, reliability, and safety in various applications. Effective quality control is essential for unlocking the full potential of AM technologies while maintaining high standards of product quality.
However, continuous improvement is also essential when assessing the quality of AM parts for a number of reasons. Firstly, AM technologies are rapidly evolving, with advancements in materials, processes, and printer capabilities occurring regularly. Stagnation in quality control practices can lead to a widening gap between existing standards and the state-of-the-art in 3D printing. By continually refining quality assessment methods, subcontract manufacturers such as 3DPRINTUK can adapt to these changes and ensure their products remain competitive, reliable, and aligned with industry best practices.
Secondly, the inherently complex nature of AM processes means that unforeseen defects and issues can arise during production. Continuous improvement allows for the identification and rectification of these issues, reducing the likelihood of defective parts reaching customers. It also helps in optimising the printing parameters, minimising waste, and improving efficiency, which is particularly crucial in production environments. Overall, embracing a culture of continuous improvement in quality control for AM parts ensures that bureaux such as 3DPRINTUK can stay at the forefront of technology, deliver consistent quality, and enhance customer satisfaction.
SUPPLIER QUESTIONS
When selecting a sub-contract 3D printing company for producing production runs of end-use parts, it’s essential for the customer to ask specific questions and evaluate the manufacturer’s responses to ensure confidence in their ability to maintain high-quality standards. By asking these questions and evaluating the thoroughness and transparency of the subcontract bureau’s responses, the customer can gain confidence in their ability to consistently deliver high-quality end-use parts for their production runs.
What quality control processes do you have in place during the entire additive manufacturing process? The bureau should describe a comprehensive quality control system, including printer calibration, material inspection, process monitoring, post-processing, and inspection protocols.
How do you select and verify the quality of the materials used for production? The bureau should explain their material sourcing practices, quality testing procedures, and provide traceability information for materials used in each part.
How frequently do you calibrate and maintain your 3D printers, and what measures are in place to ensure print consistency? The bureau should have a clear schedule for printer calibration and maintenance, ensuring precise and consistent prints.
Do you employ real-time monitoring during the printing process, and how do you handle deviations or defects as they occur? The bureau should detail their real-time monitoring techniques and how they address deviations, either through automated adjustments or manual intervention.
What post-processing steps do you perform, and how do you ensure the quality of finished parts? The bureau should list their post-processing procedures and quality inspection methods.
Can you provide documentation and traceability records for the parts you produce, including print settings, material details, and inspection results? The bureau should commit to maintaining comprehensive records, ensuring traceability and transparency throughout the production process.
Do you hold any quality assurance certifications (e.g., ISO 9001) or industry-specific accreditations relevant to our application? The bureau should provide evidence of relevant certifications and accreditations that demonstrate their commitment to quality standards.
Can you share examples of similar projects you’ve completed and provide references from past clients? The bureau should showcase their experience in handling projects of a similar scale and complexity, along with references for verification.
How do you stay up-to-date with the latest additive manufacturing technologies and continuously improve your quality control processes? The bureau should describe their commitment to ongoing training, research, and adaptation to technological advancements in the industry.
CASE STUDY
A focus on quality is critical for a company such as ecoSUB Robotics, a spin off from Planet Ocean, a specialist in the provision of high quality, marine scientific instruments for research, survey, naval and operations support. ecoSUB Robotics regularly utilises 3DPPRINTUK as a supplier for a number of key 3D printed parts. These 3D printed components have to operate in salt water, in very low temperatures, and under extreme pressure some 2,500m below sea level, while at the same time remaining water-tight and intact.
SLS 3D printed parts by 3DPRINTUK. Image courtesy of EcoSub.
ecoSUB Robotics sought a 3D printing subcontractor that prioritises quality above all else. The company’s instruments require parts that seamlessly integrate with existing OEM components and other precision-manufactured parts, such as those created through CNC machining and laser cutting. This requirement underscores the need for a subcontractor with an impeccable focus on accuracy and consistency.
The marine instruments designed and manufactured by ecoSUB Robotics are intricate assemblies where each component must align perfectly with others to ensure optimal performance and reliability. This precision is crucial for the instruments to function correctly in harsh underwater environments. Therefore, ecoSUB Robotics needed a 3D printing partner capable of producing parts with exacting tolerances and high-quality finishes. The ability to deliver parts that not only meet but exceed industry standards in terms of accuracy and durability was a non-negotiable criterion in their selection process.
By partnering with 3DPRINTUK, which is committed to exceptional quality, ecoSUB Robotics has been able to maintain its reputation for producing top-tier marine scientific instruments. The collaboration highlights the critical role of choosing a subcontractor which shares the same dedication to precision and quality, ultimately contributing to the success and reliability of ecoSUB Robotics’ innovative marine solutions.
SUMMARY
When looking to partner with an external 3D printing expert, it is important that prospective customers interrogate the integrity of the quality control system in place to ensure the viability and functionality of parts produced. Quality is not negotiable for AM parts produced for end-use applications, and as AM becomes an increasingly viable production technology, the ability to demonstrate a focus on quality control and part validation is of explicit importance.