Intelligent drive technology is the prerequisite for digitalisation and automation of production, because it enables networked or autonomous production processes in “smart factories” and keeps them running. As a leading supplier in the sector, NORD DRIVESYSTEMS provides pioneering drive solutions (hardware and software) and supports customers with its communication and application know-how for networking and connection of their Industry 4.0 environments.
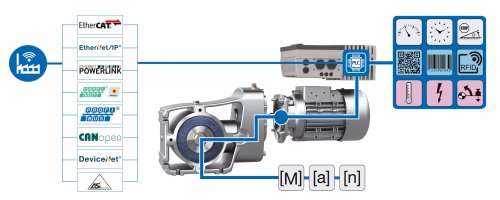
Intelligent, networked drives from NORD enable continuous condition monitoring and therefore form the basis for predictive maintenance
NORD DRIVESYSTEMS has the drive units of the future and provides its customers with intelligent digitalised production with advanced maintenance concepts and new services. All NORD drives are Industry 4.0 READY and can be directly integrated as active components in Industry 4.0 environments throughout the world. The prerequisites for this are the internal PLC as decentralised intelligence and the extensive range of communication options. The drive units are compatible with all common field buses and Ethernet-based protocols and provide analogue and digital interfaces for sensors and actuators. Thanks to the integrated PLC in the drive electronics they can provide autonomous control of sequences and movements and reduce the load on the central control system. As well as this, the drive systems are scalable, so that they can be individually adapted to the automation application with regard to complexity, quantity and size. NORD drives are prepared for integration into a cloud and can be connected to various external cloud systems.
Action instead of reaction
Fast, efficient and comprehensive evaluation of analogue and digital data by the intelligent PLC in the drive electronics forms the basis for modern maintenance and servicing concepts such as condition monitoring and predictive maintenance. Due to continuous monitoring of the field level, linking of communication, sensors, process data and vital parameters of the drive, deviations from the normal state can be quickly detected. Drive operators therefore have the possibility of responding in good time before damage or breakdowns occur. Condition-oriented maintenance replaces time-based maintenance. This results in many benefits for users such as an increase in plant availability, prevention of unscheduled down times, improved planning of service and maintenance as well as a significant reduction in maintenance and repair costs.
Virtual sensors
At present NORD is investigating sensorless monitoring of oil ageing and the condition of geared motors with virtual sensors. The aim is a predictive maintenance concept which determines the optimum oil change and maintenance intervals for each individual geared motor, oriented to the actual condition of the geared motor and the gear oil. For this, intelligent algorithms evaluate the operating data of the frequency inverter and determine the oil temperature from this information. Without the hardware costs for external sensors, oil ageing and the optimum time for replacing the gear unit lubricant can be determined with great reliability. Tests have shown that the oil temperature as measured in tests can be reliably calculated.
NORD application test area
NORD DRIVESYSTEMS demonstrates the function and opportunities of predictive maintenance, virtual sensors, drive networking and other Industry 4.0 concepts to its customers in its in-house application test area at its headquarters in Bargteheide near Hamburg. With the scalable system a large variety of operating modes and operating states can be tested in real time. Geared motors and frequency inverters can be examined or algorithms can be tested and validated under real-life conditions.