New fine-finishing face mill for cast iron exceeds highest surface requirements
Kennametal has introduced a new face milling platform for cast iron applications, the KCFM 45. With fixed and adjustable pocket seats, the new milling cutter provides the option for semi-finishing as well as fine-finishing applications, exceeding the highest surface quality requirements. With carbide, ceramic and PcBN inserts, this new tool is a flexible, cost-effective and user-friendly solution that is ideal for any type of CNC machining center.
Insert offering
Carbide inserts are ideal for machining at lower RPM, or in thin-walled workpieces and less stable conditions, while ceramic inserts (KY3500 grade) provide elevated surface speeds resulting in higher productivity. Both offer excellent performance. For fine finishing operations, PcBN inserts will deliver the best possible surface finish, tool life, and throughput.
“With the KCFM 45 face milling cutter, users can mix and match different insert options to suit the application requirements and machining conditions,” says Michael Hacker, Product Manager, Kennametal. For example, you might use PcBN finishing inserts in the adjustable pockets and ceramic or carbide inserts in all other pockets for wet machining or lower volume applications. Regardless of the configuration, the KCFM 45 exceeds the highest surface requirements.
Wave killer
The inserts are positioned at a positive axial angle, but with a slightly negative radial angle for better tool life. That creates significantly lower machining forces than competing cast iron face mills, helping to eliminate chatter and further improving surface finishes.
“The KCFM 45 with its adjustable pocket seats can generate surface finishes of 0.8µm Ra (32 µin.) or better, and waviness lower than 10µm Wt (400 µin.),” says Hacker.
The KCFM 45 is ideal for gray cast iron, CGI applications, semi-finishing and fine-finishing operations.

The KCFM 45 uses a combination of hexagonal semi-finishing inserts in the fixed pockets together with square finishing inserts in the adjustable pockets with cartridges.
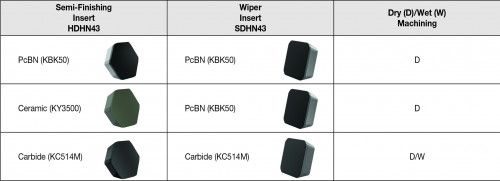
Recommended insert configuration for dry and wet machining.
Carbide inserts: Ideal for machines with lower spindle capabilities.
Ceramic inserts: For highest productivity, ideal for semi-finishing.
PcBN inserts: For highest productivity, ideal for fine-finishing.