In an exciting new project involving technical injection moulding firm Broanmain Plastics and compliance fire safety specialist Fireco, healthcare, residential, education, leisure, hospitality and industrial facilities will soon have an innovative new fire-compliant magnetic door device to choose from.
A premium and unique door release concept, the radio-activated DorMag Pro is gearing up to roll off production lines this summer at Dorking-based Broanmain Plastics. This follows on from months of both companies pooling their engineering, materials, processing and tool development expertise to refine the new products’ safety attributes.
Fireco – recently acquired by the Lagercranz Group – specialises in the design, engineering and manufacture of products to meet complex fire safety compliance requirements. Brighton-based, their flagship Dorgard product range is being expanded with the launch of a revolutionary magnetic fire door device, comprising a number of aesthetically pleasing and practical safety features.
Designed to hold fire doors open to improve access and building ventilation, yet close automatically when a fire or intruder alarm is activated, DorMag Pro answers customers calls for a sleek-looking, less obtrusive radio-activated device that is located behind the door rather than in front. The concept – initiated during the pandemic lockdown – has swiftly moved from 3D printed prototypes to a milled CNC tool, to the design and manufacturing of seven component tools. Driven forward with the assistance of the Broanmain engineering and processing experts Kamil Stec and Thomas Catinat.
Fireco’s Supply Chain & Production Manager Mark Challacombe initiated the introduction to Broanmain, confident that the technical moulding firm had the right ethos, responsiveness and expertise to support their DorMag Pro project from the latter phase of development. “Knowing that the unit needed to be plastically moulded, we commenced a comprehensive supplier review. Broanmain came out on top of our supplier matrix. They ticked every box,” affirms Mark.
“The team proved themselves straight away, refining the design and sharing their processing knowledge. Broanmain is a good fit, in that they provide all this tool making expertise, deliver a personalised service, yet also have the manufacturing capacity to scale up production to meet our market demands,” expands Fireco Engineer Matt Ball.
No alarm bells
Cost and scalability were major considerations for Fireco. Injection moulding the seven components that make up the DorMag Pro housing was deemed the most viable way to manufacture the volumes that Fireco estimates ramping up to. Matt continues: “Given our market expertise and the reaction at several events earlier this year, we anticipate incrementally increasing production and refining the build process as sales scale up. The market potential for this product range is huge, especially when combined with another acoustically rather than radio activated fire alarm innovation we are looking to release around the same time, DorMag SmartSound.”
“Injection Moulding in these volumes is far more cost efficient that 3D printing and CNC milling. It also gives us the repeatability and tight tolerances required for a compliant fire product, combined with the premium brand finish,” adds Matt.
Integral to the high-spec door release design aesthetics is a metallic-looking silver band wrapping around the device’s wall-mounted housing. However, as a radio-activated device, this strip needed to be in a non-metallic material. To meet Fireco’s high-quality design aspirations, Broanmain pulled in the expertise of a long-standing decorative partner that they knew could replicate the metallic band with a professional finish – Oldbury-based Applied Coating Technologies (ACT). “Achieving this professional-looking silver band finish on every plastic housing unit was one of the main deal-breakers in our DorMag Pro project plan,” notes Matt.
Thrilled to apply their coating expertise to the project, ACT Sales Manager Dominique Johnston comments: “Helping our customers to realise their design aspirations is the role we enjoy most. Especially when it draws on our extensive experience to define a customised finish that meets all stakeholders aesthetic, functionality and pricing expectations. Supporting the design and development of this project has been a privilege and we look forward to moving into on-going production. Seeing the parts we have coated in operation always gives us a huge buzz.”
Collectively, Fireco, Broanmain and ACT have combined years of industry know-how to overcome a number of technical challenges, affirms Dominique.
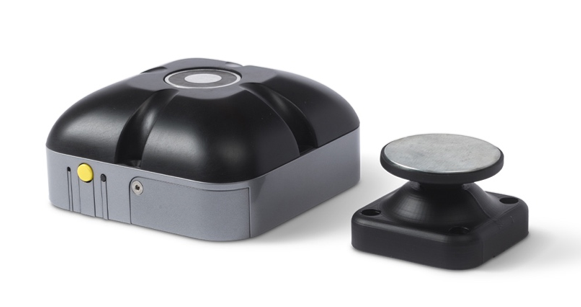
A premium and unique door release concept, the radio-activated DorMag Pro is gearing up to roll off production lines this summer at Dorking-based Broanmain Plastics.
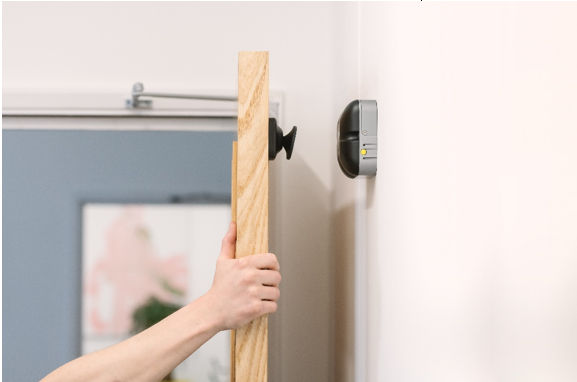
DorMag Pro is designed to hold fire doors open to improve access and building ventilation, yet close automatically when a fire or intruder alarm is activated,
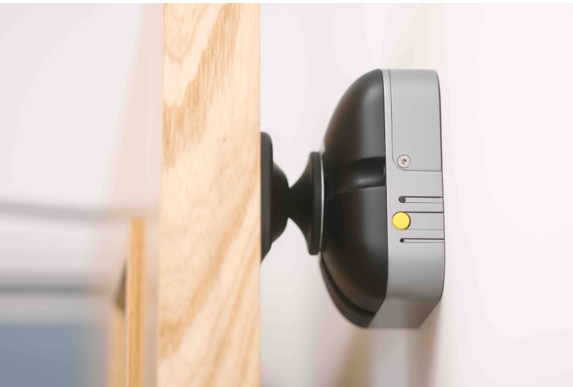
DorMag Pro is designed to hold fire doors open to improve access and building ventilation, yet close automatically when a fire or intruder alarm is activated,
Opening new doors
All of the unit’s seven components are moulded to the highest precision on two-cavity mould tools using a standard ABS material. Rigid, versatile, and high strength, the lid and base is the only component modified to ABS PC to withstand the BS EN 1155[i] durability test cycles and the impact of the fire door being smacked back into the unit.
As well as mass-moulding the seven components, Broanmain will undertake some of the specialist finishing tasks, including heat staking a metal clip onto the battery carrier and overseeing the paint finish. Fireco will assemble all the internal components, including fitting magnets and the PCBs in-house. Every element must be moulded with absolute precision to meet the tight tolerances.
“From the sleeve within the main lid to the outer channels, there’s no room for production variables. It’s why we opted for injection moulding. It’s a process that delivers absolute precision at the best price,” emphasises Matt.
Right now, the volumes don’t justify implementing a full Kanban production stock management arrangement with Broanmain. This could soon follow.
If the market interest expressed at recent fire safety exhibitions is anything to go by, the potential global reach for DorMag Pro is massive, claims Mark. “Fire legislation is a constant moving target. Being part of the Lagercranz Group provides lots of in-roads into Europe. Although this magnetic door release system leans more towards the premium market, the way we have engineered it so it can be positioned unobtrusively anywhere away from the hinge on the rear fire door, opens up a whole new market of opportunities,” reports Mark.
About Broanmain Plastics
From high volume production runs to precision moulding, CNC finishing and assembly, Broanmain Plastics is one of the few UK plastic specialists to offer all of the design, moulding and setting techniques, prototype development and distribution services through one facility. Fully project managed by technically competent industry, materials and application experts. Broanmain was founded in 1956 and remains a family-run business.
Broanmain Plastics, Forge Works, Horsham Rd, Dorking RH5 4EJ