Shock and vibration-resistant absolute rotary encoders from Wachendorff Automation are providing precision position feedback for the automated feeding of pipe components as part of a control system on AT-Boretec’s horizontal boring machines. Providing a cost effective alternative to traditional trench digging methods for laying broadband services, water supplies and other underground systems, these mobile construction industry machines operate under harsh environmental and mechanical conditions where reliability and long trouble-free working life are of prime importance. Represented in the UK by Variohm EuroSensor, Wachendorff is a technology leader in automation measurement systems with a comprehensive standard range of incremental and absolute encoders and a customisation service for demanding severe-duty position measurement tasks across all industries.
Powerdrill and Rockdrill series self-propelled horizontal drill rigs from the German manufacturer AT-Boretec are available in a wide range of scaled tonnage classes. Characterised by easy loading of drilling and reaming tools and pipeline sections for fast execution of multiple drilling operations, the machines cater for everything from small diameter pipelines for fibre optic cables to large bores for wastewater drainage systems. Especially cost-effective and speed efficient where pipelines need to be located under roads, buildings and other sealed-surfaced sites, the machines can bore up to several hundred metres horizontally with a drilling and flushing process that employs a combination of drill heads and reamers to expand the bore and when required to deliver sections of pipeline. Each machine is equipped with 40 to 70 ‘drill pipes’ stored in a side-mounted magazine with lengths varying from three to four and a half metres – which are removed using a gripper unit, then assembled on special drilling carriage and bolted to the drill pipe already located in the ground.
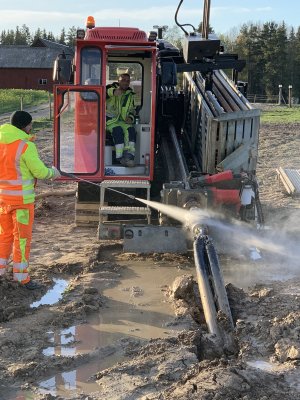
Image: AT-Boretec’s horizontal boring machine in action
Whereas previous generation machines from AT-Boretec required the operator to leave the cabin and manually unlock each magazine row, thanks to the automation of the magazine unit, the latest Powerdrill series allows the correct row to be conveniently preselected for automatic drill pipe removal via a cabin-mounted touchscreen console – thus saving considerable time and allowing more comfort and safety for the machine operator. As part of the new control system a Wachendorff WDGA absolute encoder is used to provide the row position via its integrated CANopen interface to ensure the gripper makes the exact alignment for the procedure.
The encoder specified for the magazine is a customised version of Wachendorff’s WDGA series, parameterised for an 18 bit multi-turn configuration to provide more than sufficient resolution and measurement range for the task in hand. The selection mechanism is driven via gear reduction with the encoder mounting effectively decoupled via spring-toothed wheel design to minimise unwanted forces on the sensor’s shaft and specially adapted bearing system. The highly precise, dynamic and robust WDGA series is extremely capable of withstanding the exceptionally shock and vibration levels encountered on the machine where shaft loads of 120 N axially and 220 N radially are easily supported. The WDGA series absolute encoder supplied to AT-Boretec also includes the IP67 environmental protection option as well as additional shaft sealing and, although subjected to extreme weather conditions as well as the mud and dirt deposits due the drilling process, is installed on the machine without the need for additional protection. Two IP67 rated M12 connectors allow easy machine integration for encoder power and CANopen communications. As a standard feature, and for added operational safety as well as fast fault diagnosis, the WDGA includes a status LED integrated in the housing. And of course, absolute positional feedback technology also allows the machine to be set-up without the need for home sensors on start-up or in the event loading problems and subsequent resetting procedures.
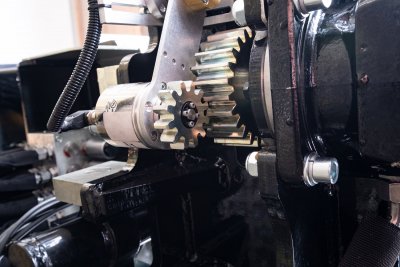
Image: Wachendorff’s customised WDGA absolute encoder in-situ – mechanically decoupled to reduce unwanted forces on the sensor axis and installed without any further protective enclosure
The WDGA series, as standard, features Wachendorff’s patented EnDra® and QuattroMag® technologies where a unique non-contacting coded magnetic signal for each individual 4096 counts/rev rotation and for each accumulated revolution does not rely on internal gears or batteries – guaranteeing extremely long life and exceptional levels of reliability over operational temperatures of -40 °C to +85 °C. The standard range covers 36 mm and 58 mm housing diameters with 16/43-bit single-turn/multi-turn resolution and a choice of synchro flange or clamping flange mountings.
The CiA 301 CANopen device profile provides position, speed and acceleration information with many other features such as heartbeat, node-guarding, scaling and extensive diagnostics with up to 4 transmit PDOs individually configurable. Other WDGA series encoders from Wachendorff offer RS485, SAE J1934, SSI, Profibus, ProfiNET, EtherCAT, as well as Universal IE and other interfaces to ensure flexibility across a very wide range of machine architectures. Wachendorff also design and manufacture highly robust incremental encoders and a wide range of application matched measurement systems.
Variohm EuroSensor supplies and fully supports Wachendorff’s complete range of absolute and incremental shaft encoders and measurement components.